My plant is tripped - Ensures power supply to critical processes
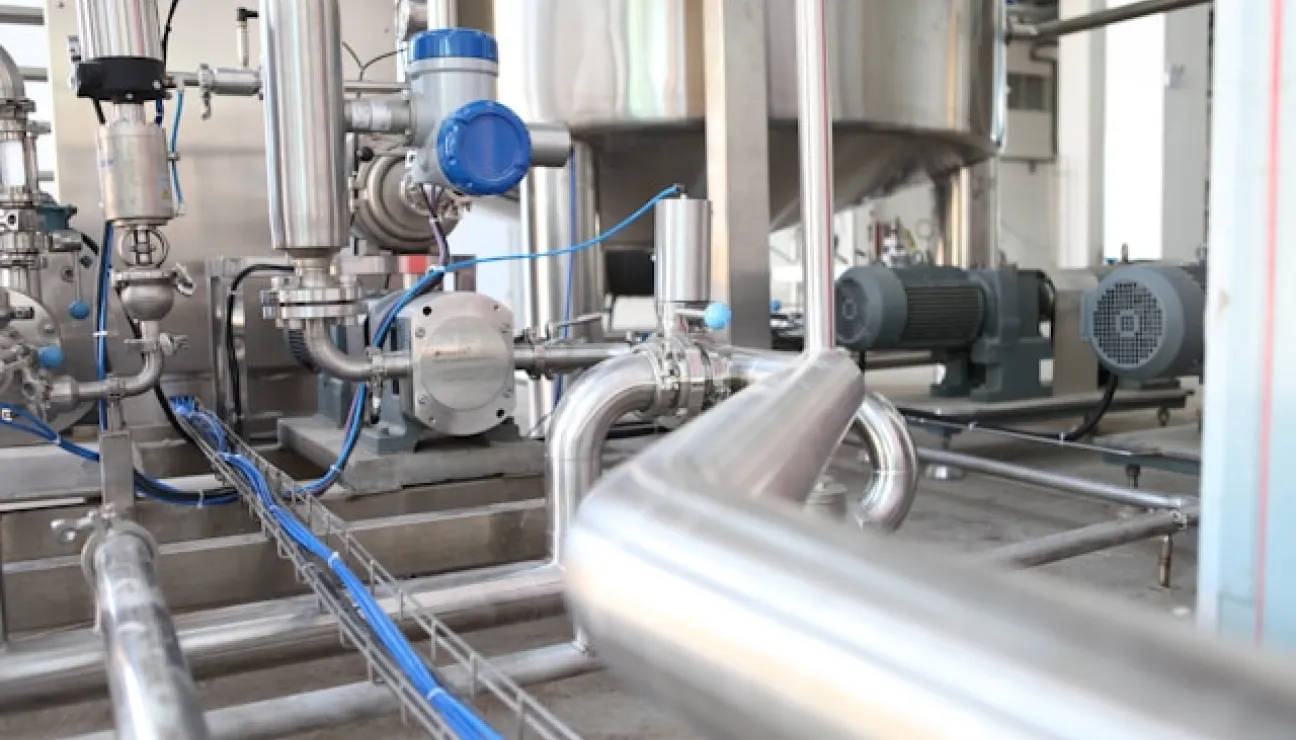
How to ensure the power supply of critical industrial processes for all those applications that require uninterrupted and quality power supply? The truth is that an outage lasting a few seconds can mean much more than a momentary lapse in production. An incredibly brief loss of power can cause serious damage to sensitive equipment, machinery, end products and materials, and what's involved is a subsequent restart, which can be time-consuming and costly. This results in economic losses due to production downtime and machinery damage and headaches for managers and plant managers of businesses affected by this problem.
When do I have to worry?
Sometimes the solution is to stop production completely and restart it again. However, this is not always possible due to its high economic cost. We are talking about production processes in which it is very expensive to stop and restart production, such as in electric arc steel foundries; in those industries in which the processes must be continuous because it is detrimental to the final product or causes damage to the machine.

In these cases, the first step must always be to discover the cause that is producing these stoppages. The big question: Is the disturbance generated by my installation or does it come from the outside? Sometimes this problem comes from the quality of the external network and must be worked on at the border between the plant and the external electrical network. Other times, it has to do with the operation of the plant. In this case it is worth asking: what signal distortions are being generated by my equipment or electronics? Are the protections correctly selected for the loads they have today?
Start by measuring and sizing the protections
The first case is to measure, from the level of the switchboard to the entire plant system, to identify the critical points that cause the outage to propagate. It is likely that the outage is occurring on one machine and the fault is elsewhere. This phenomenon is probably due to a bad dimensioning between the loads and the existing protections. After this first phase, it is essential to make an inventory of both the type and the rating of the loads and to check with analyzers that the protections are well selected and coordinated with each other. A successful analysis in this sense can ensure a satisfactory result which, depending on the magnitude of the outages, can reduce outages by up to 60%, with all that this implies in terms of economic savings and efficiency of the production processes.