CIRCE, at the forefront of recycling technologies
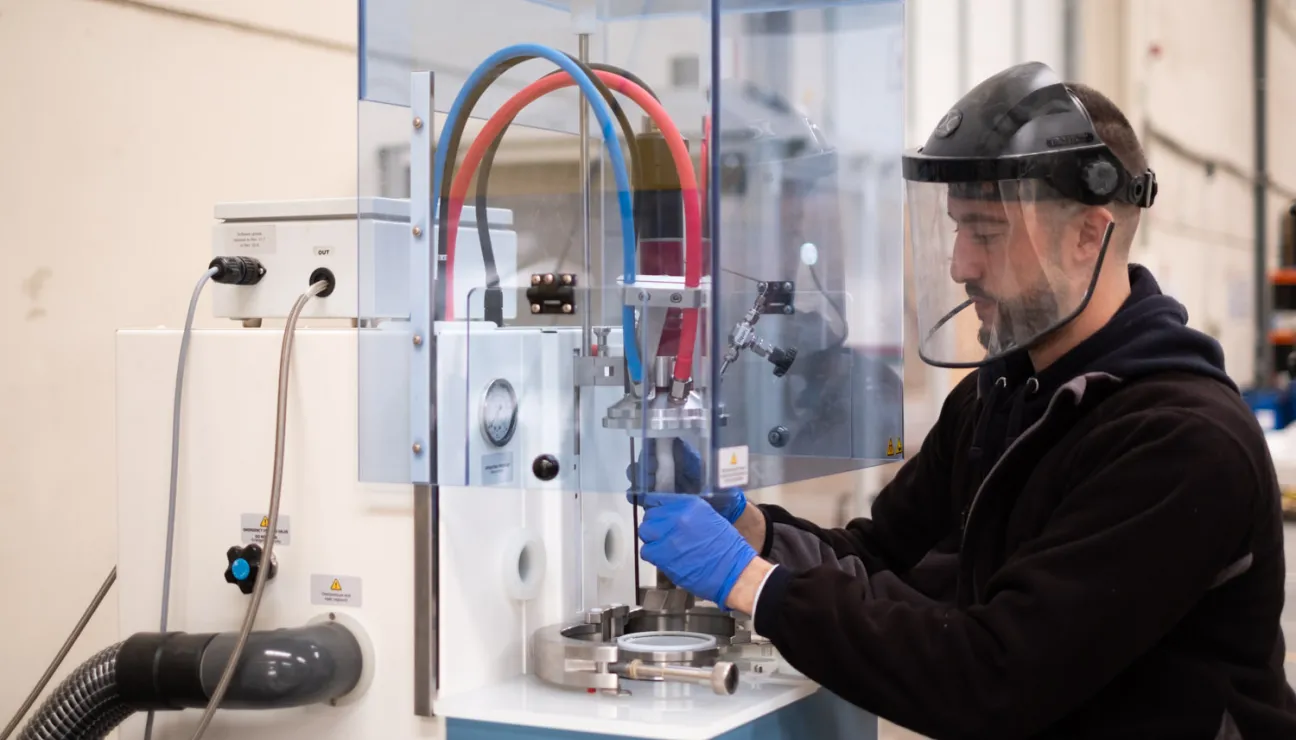
Proper waste management is crucial for companies, not only because of the environmental impact, but also because of the legal and economic implications. Adopting responsible recycling and reuse practices contributes to sustainability, improves corporate reputation and can generate significant savings in raw material costs. However, the challenge lies in implementing efficient technologies and complying with increasingly stringent regulations, while optimizing processes to reduce the environmental footprint and transform waste into usable resources.
The CIRCE Technology Center, in collaboration with international companies and consortia, has long been developing innovative technologies to transform different types of waste into reusable resources, with the aim of promoting the circular economy and reducing environmental impact. These technologies cover various sectors and materials, from batteries and electronic waste to plastics and textiles.
Solvolysis and microwave pyrolysis
Wind farms and photovoltaic farms face significant challenges at the end of their useful life (around 30 years), mainly related to the high costs of decommissioning the farms, bureaucratic schemes and waste management. The recycling of wind turbine blades and solar panels faces a major challenge mainly because of the large accumulation of waste that will be generated. The high targets for the revaluation of Waste Electrical and Electronic Equipment (WEEE), including solar panels, and the landfill bans, require a solution for the recycling of such waste. That is why CIRCE is working on recycling processes that allow the recovery of materials with high added value.
In the case of panels, thermal recycling allows the extraction of glass and aluminum, which make up about 83% by weight of the panel and which allows the recovery of the copper wires that connect the photovoltaic cells. There is a high added value in the components of this cell as it contains silicon and silver that can be extracted by hydrometallurgical methods. CIRCE has managed to extract 100% of the silver and is working on the purification of silicon to reach metallurgical purity (99.9999%).
In wind turbine blades, the added value lies in the recovery of glass or carbon fiber, which is used as a structural agent to increase the strength of the blades and reduce their weight; these materials are called composites. This fiber is embedded in resins that must be degraded during the recycling process. CIRCE uses microwave-assisted solvolysis and pyrolysis technology. Solvolysis works at around 200 degrees Celsius and allows the recovery of the fibers by degrading the resin into its main organic compounds. This same technology can be applied in the recycling of other types of composite waste generated during building demolition. Pyrolysis, however, works at higher temperatures (450 - 700ºC) and releases the glass or carbon fibers by degrading the resin into gases that condense into high value-added chemical building blocks .
The main advantages of microwave technology are short processing times and the use of electricity for its operation which reduces dependence on fossil fuels. That is why CIRCE also uses this technology in the recycling of textile waste. The objective is to accompany companies in the process of decomposing polyester textiles by means of microwave-assisted glycolysis, allowing the recovery of their original components and their reuse in new products.
In addition to waste management, CIRCE focuses on the eco-design of products to facilitate their subsequent reuse and on new recycling technologies that are more efficient and have a lower environmental impact than traditional methods.
The challenge of recycling batteries
With battery recycling as a priority, CIRCE uses hydrometallurgical processes to recover key materials such as lithium and cobalt, which are essential for the production of electric vehicle and industrial batteries. This approach reduces reliance on mining for new materials, especially with China, and is in line with targets set by battery regulations that will be mandatory by August 2031 and will include minimum recycling rates for cobalt (16%), lithium (6%) and nickel (6%).
In the case of batteries, many of their components (active materials and electrolyte) can contaminate soil and water if not properly managed, in addition to causing toxic emissions and fires. Current recycling processes are largely not optimized to deal with the growing volume of batteries at the end of their useful life, which underlines the need to implement advanced and versatile technologies, such as hydrometallurgy that CIRCE is working on, to ensure efficient and sustainable recycling. Learn more about waste recycling, from batteries to wind turbine blades.
.jpg)
Latest news
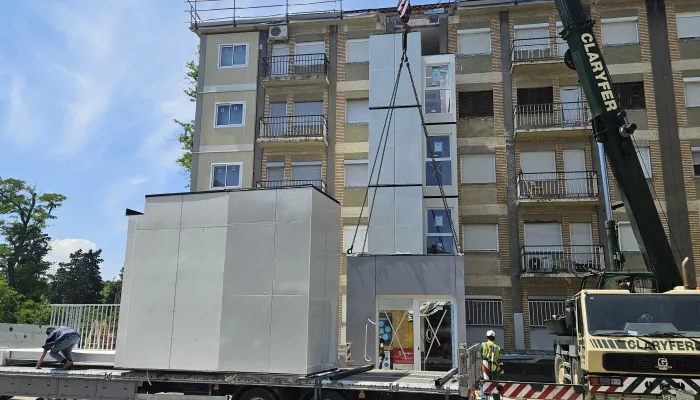
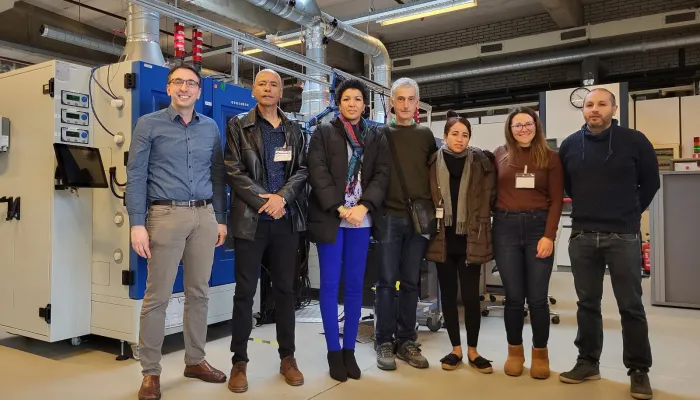
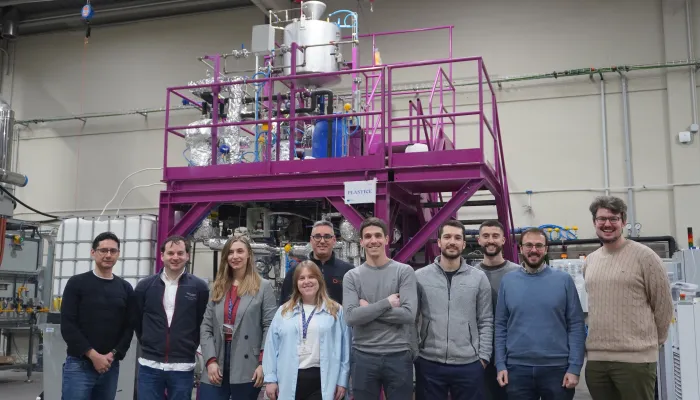