The economic and energy efficiency behind induction thermal processes
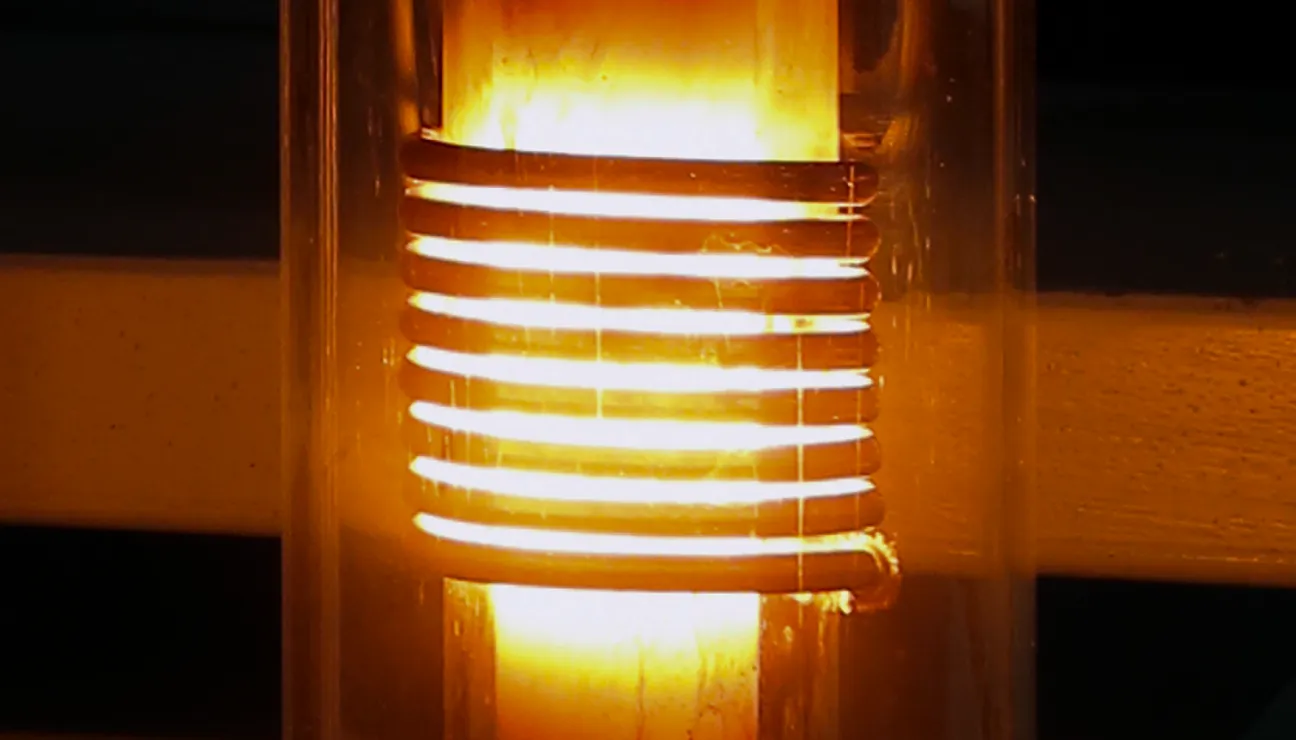
The Great Challenge of Industrial Electrification
Decarbonization is one of the key challenges facing our country's industrial sector. Electrifying industry is becoming a cornerstone in guiding energy-intensive companies toward efficiency and sustainability.
This shift introduces a new technological paradigm, providing an alternative to fossil fuel sources, such as gas, by adopting renewable electric sources. It’s a new scenario that drives change not only in Spanish industry but also across Europe, aiming for climate neutrality by 2050 as outlined in the European Green Deal.
Thermal Processes: Essential for Energy-Intensive Industries
In industries like metallurgy, chemicals, and automotive, efficient thermal energy management is essential—not only to ensure product quality but also to optimize energy consumption and reduce environmental impact.
With industry consuming one-third of global energy and heat generation accounting for three-quarters of that, addressing this challenge is urgent, especially when climate neutrality is defined by the European Council as emitting less and absorbing more, focusing on high-emission industries.
Thus, it’s particularly relevant to examine the potential impact of electrification in the industry.
Electrification Solutions for Industry
Focusing on heat production, 50% currently comes from direct fossil fuel combustion, with only 32% from electrical sources. Additionally, energy demand in the sector is expected to double by 2050. The urgency to shift from traditional heating systems to more sustainable ones, without compromising profitability, is increasing.
Aware of this, CIRCE works to transform resource usage and develops innovative tools to enhance company competitiveness. To this end, it has developed a calculator enabling industries to evaluate the economic and energy savings they could achieve by replacing gas heating with induction technology.
The tool's goal is to assess the profitability of this change, helping companies optimize their thermal processes and supporting them through the electrification journey, from techno-economic evaluation to real-world implementation.
The tool is highly user-friendly: users input industrial data, such as part size, temperature, heating duration, and payback time. Within minutes, it calculates total cost, energy consumption, and necessary coil size. This way, companies can minimize annual heating costs while gaining economic savings from reduced energy consumption and generating Energy Savings Certificates (ESCs), which add economic value to the total savings achieved.
This tool optimizes the calculation process, achieving speeds up to 80 times faster than traditional multiphysical calculation tools.
With this solution, calculating the optimal induction heating system for a process not only reduces the necessary time but also cuts operational costs.
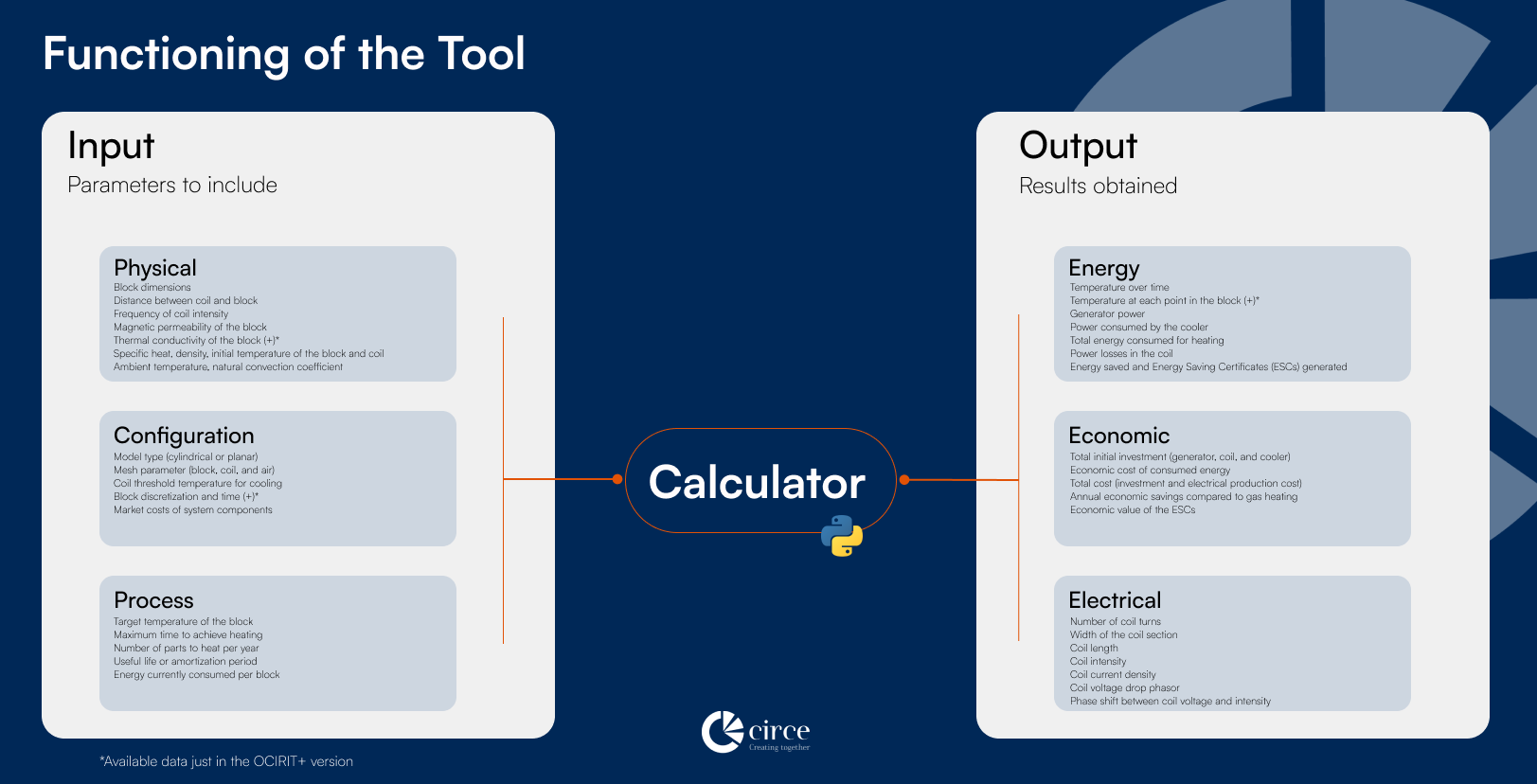
Currently, the calculator offers two approaches:
- A detailed view that provides an advanced estimation of economic and energy savings, supporting the optimal selection of an induction heating system.
- Another version that, in just 1 second, offers a preliminary view of power, energy, and savings requirements, facilitating integration with decision-making and energy management systems, including digital twin applications.
With this calculator, industries can reduce the environmental impact of their heating processes while achieving up to 70% in energy and economic savings.
Success Story of the Thermal Optimization Tool in the Market
This tool is ready for use and has already demonstrated results in a real energy efficiency case.
With an industrial company, we analyzed its heating process costs. This company had high demand as a manufacturer focused on automotive and electric mobility sectors, with over 60 production plants.
We found that our client was consuming 17 kWh with gas. Using the tool's calculations, we optimized the process to an induction heating system consuming only 5.6 kWh, achieving a 67% improvement in both energy and cost efficiency by operating at constant power.
At CIRCE – Technology Center, we have 20 years of experience in inductive power transfer systems. Want to learn more about our optimization and energy efficiency tools? Contact us directly.
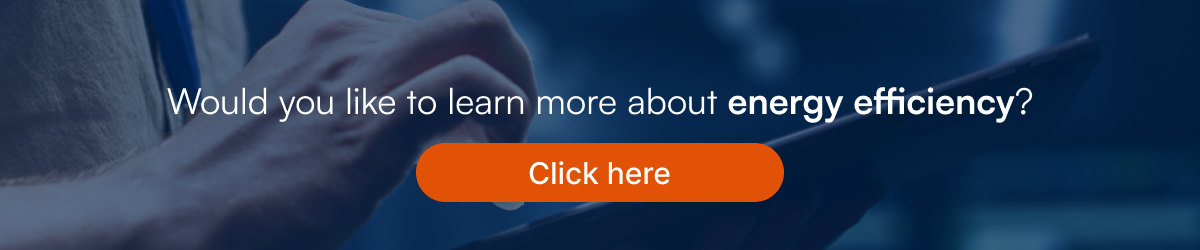