Ebroacero collaborates with CIRCE to improve energy efficiency in its plant
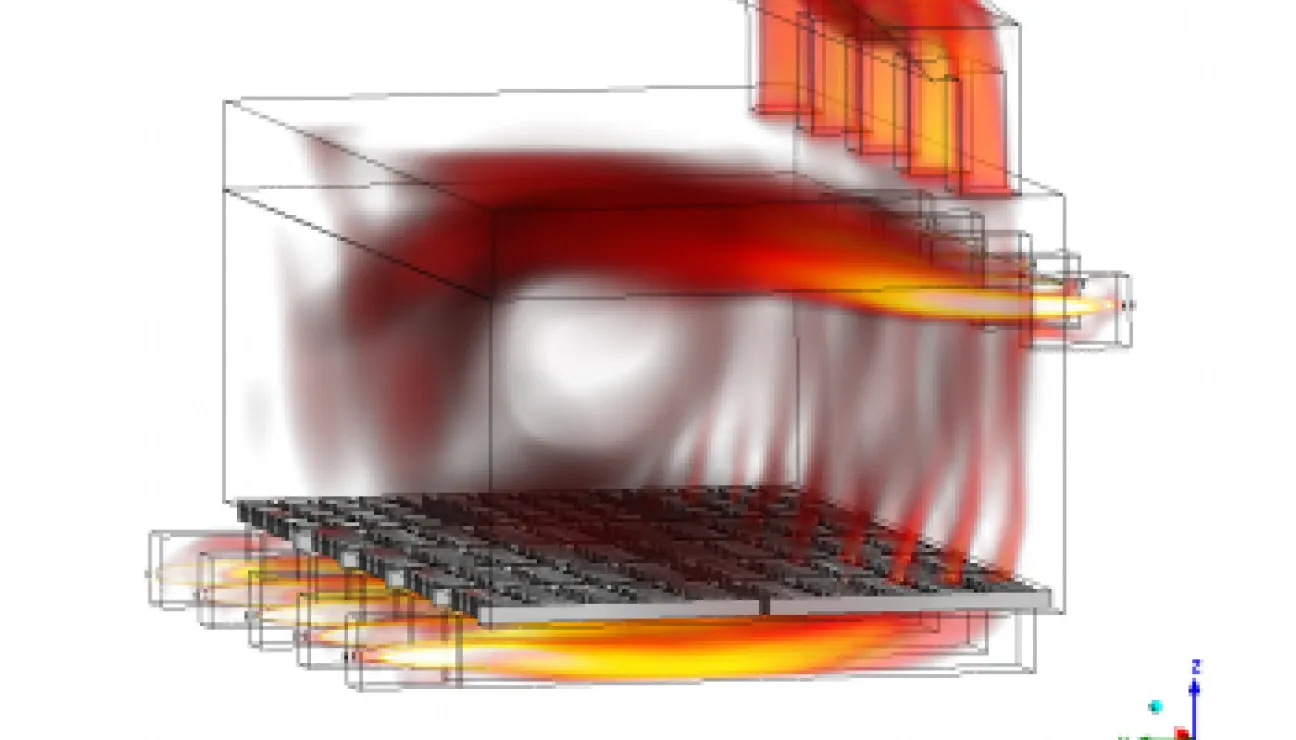
Energy is a key factor for the competitiveness of companies, especially in industrial sectors that are intensive in the use of this resource. These industries, above all those that are committed to the internationalization of their products, are particularly affected by the escalation in prices and environmental impact. Aware of this, the Aragonese steel industry Ebroacero has begun a process of improvement by installing a system in one of its furnaces that increases the energy efficiency of the entire process and expands its production capacity. This has enabled it to increase its customer portfolio, taking on larger jobs more quickly.
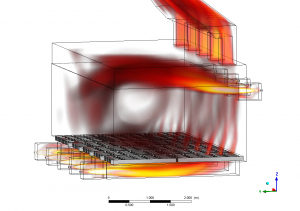
This has been possible thanks to the collaboration with the CIRCE technology center, which has made it possible to improve combustion efficiency, reducing gas consumption and increasing the quality of the treatments by homogenizing the temperature inside the furnace. As a result, thermal losses have been reduced by 59% thanks to a new wall lining that improves insulation and the modification of gas recirculation, increasing the heat exchange between the gas and the parts.
This project has enabled Ebroacero to increase its competitiveness, improve process efficiency and, in turn, its carbon footprint, as well as increase productivity and reduce delivery times, key elements for competing with the major global players in the sector.
As the heat treatments of the furnaces are long, ranging from 12 to 22 hours, great savings in fuel consumption have been achieved, as well as reducing the emission of polluting gases into the atmosphere, thus contributing to a more economical and cleaner operation.
Use of CFD fluid simulation technology to achieve these results
In this type of process, the final quality of the material requires homogeneous and controlled heating. After the modifications, the surface temperature distribution of the parts has improved significantly, dropping from differences of around 85 degrees Celsius to values between 30 and 40 degrees Celsius.
All this makes it possible to carry out treatments at high temperature (900 degrees Celsius) and at medium temperature (600 degrees Celsius), ensuring maximum quality in the parts. This improvement process has been possible thanks to the CFD (Computational Fluid Dynamics) fluid simulation technology developed by CIRCE.
Thanks to this tool, which works as a digital test bench, it has been possible to optimize designs and processes on an industrial scale without affecting the daily operation of the plant, saving costs in the redesign phase of the installation and shortening lead times until the production phase.
About Ebroacero
EBROACERO, S.A. is a foundry that works in the supply of castings and machined parts for different international markets. One of the most evolving markets, and therefore the most competitive, is the offshore market with large projects for offshore oil and gas extraction, as well as wind farm projects in this sector. This market requires the manufacture of castings with high mechanical requirements due to the high demands to which the parts are subjected.