NIWE
Relevant project information
Dates
Project website
Role of CIRCE
Grant agreement number
Funded by
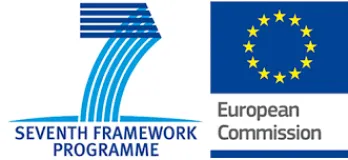
Description and objectives
The NIWE project will demonstrate a new production process capable of reducing the energy required to obtain foundry products by more than 25%, drastically reducing the associated carbon emissions.
The materials for which the process will be optimized will be aluminum, iron and steel.
The expected increase in process efficiency is due to a new furnace that, through an induction-based drive system, will allow much more flexible production.
This increase in production flexibility is in line with the current variability of demand for foundry products.
The current crisis has generated a great variability in demand, both in terms of quantity and product diversity.
Producers are forced to frequently start and stop their production lines, changing molds and, most relevant in terms of energy loss, reheating large quantities of raw materials several times. As a result, the economic benefit of the process has been greatly reduced.
NIWE addresses these problems by providing a new type of furnace that will be powered by an inductive coupling, which will provide a fast transmission of energy from the grid to the furnace itself. This energy will be transmitted to the thermal system by means of resistors or inductive heating.
Value proposition
The speed of the power transmission system, as well as the wireless operation, will allow the use of smaller furnaces, thus favoring lower overheating of raw material and energy savings.
In addition, by not needing cables, the furnaces will be able to operate with greater flexibility, facilitating a quick change in the foundry's operating scheme, since it will be based on interchangeable furnaces of different types and sizes, depending on demand.
NIWE's main objective is to develop and demonstrate new processes and equipment for metallurgical intensive industries (namely aluminum, iron and steel), to reduce energy consumption related to the smelting and production processes, as well as GHG emissions by reducing the carbon footprint of the products.
The expected results after completion of the project are:
- Recommendations for new processes and equipment.
- New integral design of processes, materials and equipment for aluminum, steel and iron demonstrators through simulation.
- New detailed concepts and methodologies for production processes in the metallurgical industry.
- Construction of the three demonstrators
- Operation guides for the new processes and equipment
- Definition of new production models
- CIRCE designs, builds and tests the IPT (Inductive Power Transmitter) prototype. This includes power electronics, shielding and thermal development.
- CIRCE is also involved in dissemination and monitoring activities, as well as LCA and LCC studies.
- In addition, CIRCE provides engineering for prototype scale-up to industrial demonstrators.
Project partners
Tecnalia, Sematec, CIRCE, the iron foundry Furesa, Deguisa, Krown, Ondarlan (Inductotherm Group), the steel foundry Bilbolul (Bulgaria), the aluminum foundry Fonderie 2A (Italy) and AFV.