Hornos industriales más eficientes para mejorar la competitividad de la industria europea
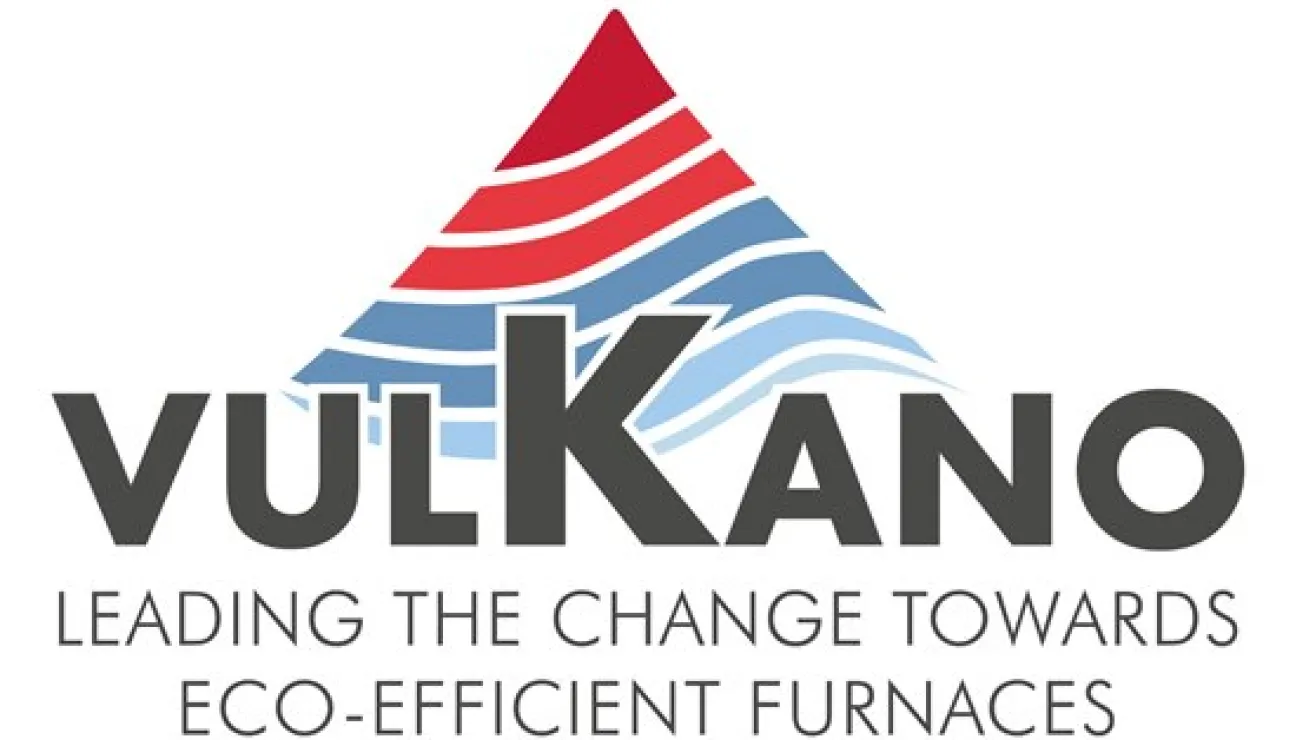
Las industrias intensivas de energía se enfrentan constantemente ante nuevos desafíos para incrementar la eficiencia, fiabilidad y flexibilidad de sus procesos. Concretamente, los procesos que incluyen hornos industriales son los que destacan por sus altos consumos energéticos, por lo que han sido el foco de numerosas investigaciones encaminadas a mejorar la sostenibilidad y competitividad de todo el sistema.
Para contribuir a este objetivo surge el proyecto VULKANO, que pretende diseñar, implementar y validar soluciones innovadoras y su integración conjunta para impulsar e incrementar la eficiencia, tanto energética como medioambiental, de los hornos industriales alimentados con gas natural y sus procesos adyacentes. La iniciativa está financiada por la Comisión Europea con cerca de 7 millones de euros y está coordinado por CIRCE.
Durante los tres años y medio de ejecución de VULKANO, CIRCE liderará un consorcio de 12 socios procedentes de Eslovenia, Francia, Italia, Reino Unido, Polonia, Alemania, Turquía y España que pretende propulsar el sector industrial europeo. El proyecto VULKANO se centrará en la modernización de los dos tipos de hornos industriales más usados en la industria, los utilizados en las fases precalentamiento y de fusión, que se emplean en dos sectores intensivos en el uso de energía (acero y cerámico), analizando su viabilidad de replicación en otro sector clave como es el del aluminio.
En estos hornos VULKANO espera conseguir un incremento del 20% de su eficiencia global y al menos un 27% de ahorro de combustibles, lo que supone una reducción en los impactos ambientales asociados.
Soluciones refractarias para hornos industriales
Alcanzar estos objetivos será posible gracias al desarrollo e integración de cinco estrategias innovadoras. Por un lado, se desarrollarán tecnologías basadas en materiales de cambio de fase para almacenar y reutilizar la energía recuperada del proceso aguas arriba y abajo del horno, así como nuevos refractarios que permitan vencer las actuales limitaciones existentes de estos materiales en cuanto a durabilidad y mejoren la eficiencia energética específica del horno.
Además se espera reducir hasta un 40% el gas natural empleado por otro procedente de fuentes alternativas o renovables. Así, se diseñará un nuevo quemador o se adaptarán los existentes, para que puedan utilizar un syngas obtenido a partir de biomasa u otros gases recuperados del propio proceso.
Por otro lado, se desarrollará un sistema de monitorización y control que permita incrementar la eficiencia global resolviendo los problemas de integración de los subsistemas individuales.
Por último, el proyecto también desarrollará una herramienta holística predictiva que permitirá obtener una mayor optimización de los procesos, mediante la integración de las nuevas soluciones a lo largo de la cadena de valor de los procesos asociados al horno.
Esta herramienta de predicción será de gran ayuda para la toma de decisión por los operadores de planta, a la hora de elegir las estrategias de readaptación, fomentar la eficiencia global, incrementar la competitividad y reducir el impacto medioambiental de la cadena de valor del producto, siempre teniendo en cuenta el ciclo de vida completo del sistema y el coste-beneficio del mismo.
Las soluciones desarrolladas serán implementadas en dos instalaciones reales, una del sector cerámico (en España) y otra del sector del acero (Eslovenia), así como validando la viabilidad de replicación de dichas soluciones en un tercer sector, el del aluminio (en Turquía). Un consorcio bien equilibrado, formado por usuarios finales, proveedores de soluciones tecnológicas y centros de I+D, garantiza la consecución satisfactoria de los objetivos, permitiendo una amplia y rápida replicación de la estrategia para la mejora de los hornos industriales europeos hacia diseños más modernos y eficientes energética, económica y ambientalmente.
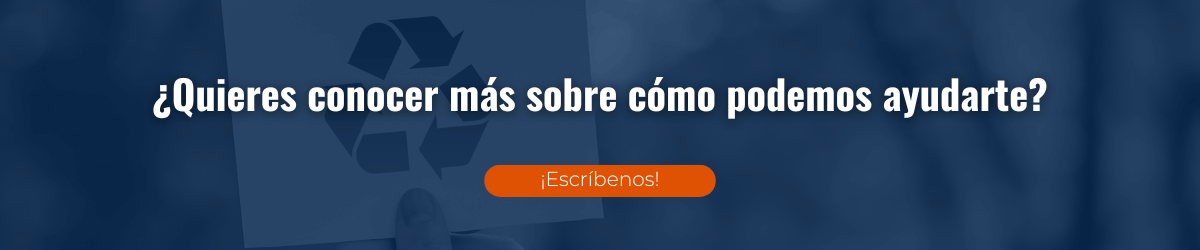